What Pad Printing Machines are right for my application?
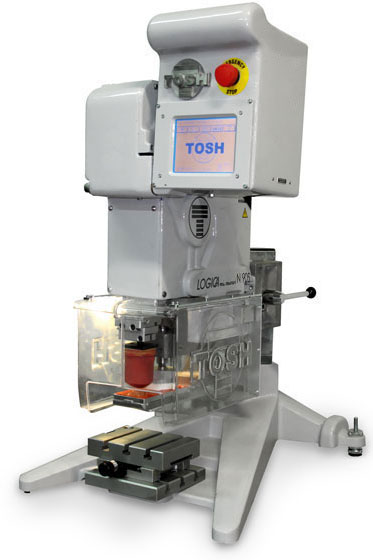
Pad printing has many uses in a diverse set of industries. The uses range from printing on toys, appliances, electronics, medical devices and even automobiles. The process of pad printing focuses on the ability to transfer a 2-D image onto a 3-D object. This procedure is completed by using an indirect offset printing process which involves the image being transferred from a cliché on a silicone pad. From this pad it is then transferred onto a substrate.
When referring to pad printing applications they fall into three primary categories:
- Printing
- Decoration
- Coding
Printing is defined as the applied application of ink onto a substrate. This is a four color process and is usually used when printing multicolor symbols and lettering. Decoration it is generally used in collaboration with a design to enhance the looks of a product. These products are asymmetrical designs with single or multicolor pigments. Coding is used for informational printing only. This type of printing will be legible but not necessarily high quality like the other methods mentioned.
So how do you know which pad printing machines to purchase? The first question might be obvious, but ask yourself, does your application actually need the pad printing process? The dimensional tolerance, surface finish and frequency of batches are the primary areas of focus when deciding if you need a pad printing machine.
Basic Pad Printing Technologies in Use Today
We now take a look at the three basic technologies that are used in pad printing today: open inkwell, closed ink cup and rotary gravure.
Open Inkwell Pad Printing
- Requires the use of a spatula and doctor blade
- Very versatile
- Utilizes a cliche holder that uses an open ink reservoir
A feature that is commonplace with all machines is the need to flood the cliché image with ink. After this you need to doctor it clean. This type of machine uses a spatula and doctor blade. The spatula is used to flood the image with ink during the machine processing stage. The doctor blade then clears the excess ink from the surface of the printing plate. At the same time the machine completes this without removing the ink from the etched area.
Closed Ink Cup Technology
- Universally used
- Ink is contained in an inverted cup, reducing solvent evaporation
- Does not require a spatula
Closed ink cup technology was originally introduced in the mid 1980’s. Today it has been universally accepted with customers from around the world. One of the key features that makes it so popular is that the ink is encapsulated in an inverted cup. By doing this it limits solvent evaporation. Closed ink cup technology also does not require a spatula.
Rotary Gravure Technology
- Frequently used for printing around the circumference of a circular/spherical part
- Uses open inkwells
Finally we have the RTI system (otherwise known as rotary gravure technology). This technology is frequently used in applications that need printing on 360 degrees around a circumference of a part. Open inkwell technology and RTI technology are similar in design as they both use open inkwells and doctor blade assemblies. A cylindrical steel drum is used for the printing plate, which contains the etch on its surface. The RTI system also features a silicone transfer pad that is circular and is made from an aluminum hub.