What is Pad Printing?
Many times, we get the question: Well, what is pad printing? If you happen to be wondering the same thing, read on!
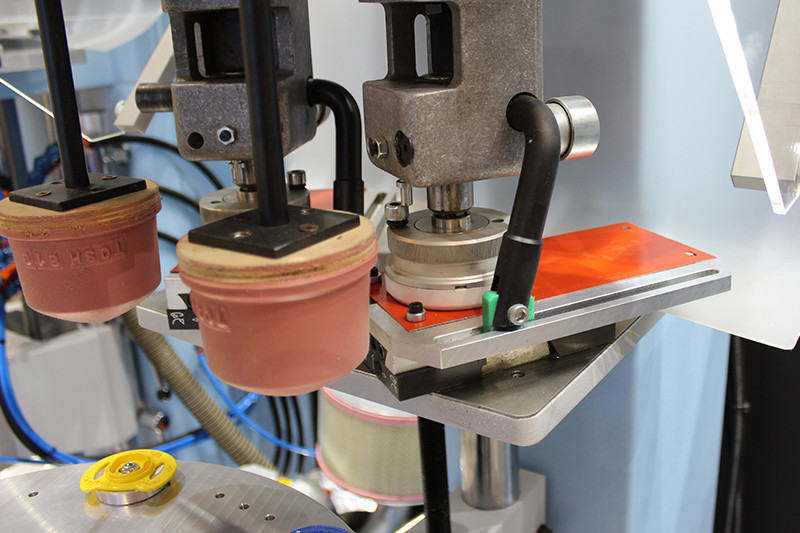
Pad printing is a modern printing process that can be used to quickly transfer 2-D images on to all sorts of 3-D objects. However, before getting into a description of what pad printing is, it’s important to first define a few specific elements that pad printing relies on.
First, it’s important to understand gravure printing. Gravure printing, put simply, is printing that etches an image onto the surface of a metal plate. This places the images – in ink form – in the recesses of the metal plate, unlike relief printing (where the image is raised). By filling the recesses with ink, and leaving the raised portions of the plate dry, the image can be transferred from the plate to the substrate quickly and cleanly. Gravure printing can produce very fine and detailed images on short or long runs in multiple colors.
Beyond the gravure printing process, pad printing also relies on printing plates – or clichés. In traditional offset printing, printing relies on transferring an inked image from an offset (the plate) to a rubber blanket which then makes contact with the print surface. When compared to other modern printing methods, offset printing with plates is one of the best solutions when it comes to economically producing commercial quantities of high quality prints, without requiring much maintenance. Today, clichés are made from metal or polyester.
However, pad printing is unique when compared to other gravure and offset printing methods in that the ink is transferred from the printing plate with a silicone pad, which then transfers the ink to the substrate. This allows pad printing to be used for printing on a number of products that would otherwise be impossible to print on, including medical products, electronics, appliances, toys, sports equipment, and more.
Crude forms of the basic premise behind pad printing have existed for hundreds of years. However, the popularity of the process enjoyed rapid expansion when the availability of modern manufacturing made widespread commercial use feasible. This expansion was felt first by the watch-making industry after the Second World War, which then gave way to pad printing being used for far more products. Since then, pad printing has experienced substantial growth due to the many applications that have found a use for it.
Partly to thank for the rapid growth of pad printing has been the increased availability of advanced silicone. The unique properties of the silicon pad in pad printing gives the process its highly sought after ability to pick the image up from a flat plate and then transfer it to a number of surfaces – including flat, spherical, textured, concave, and convex surfaces. This makes pad printing invaluable for everyone from appliance manufacturers to electronics manufacturers who need a better solution for membrane switch printing.